Modular Pallet Platform Upgrade
16th August 2023
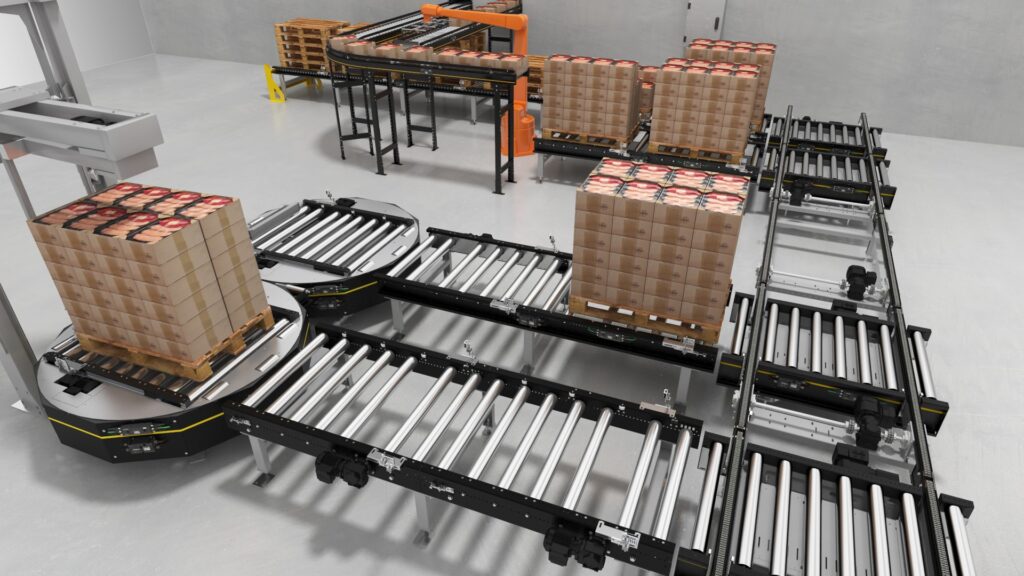
Interroll, a global leader in innovative material handling solutions, has enhanced its Modular Pallet Platform (MPP) to meet market demands for an increased load capacity, enhanced energy efficiency, reduced complexity of design and improved storage options for warehouse facilities.
Designed to revolutionise pallet handling, the MPP is a fully configurable system that offers reliable and efficient streamlined material flow. It is capable of transporting heavy pallets with ease, with a maximum weight capacity of 1,500 kilograms – increased from 1,200 kilograms. Tested to 1.5 million cycles at 1,500 kilograms, the system has been put through its paces and proven to operate without failure to the equivalent of 3 years of average use.
With a top of roller height starting from just 95 millimetres on some modules, the conveyor solution can be easily accessed by hand pallet trucks and forklift trucks, simplifying the process of loading and unloading pallets. The modular system offers a range of assembly heights and conveyor widths to fit individual customers’ specifications. Its Pallet Drive conveyor is available in a flat version with an integral motor. This saves space, reduces maintenance, and simplifies the conveyor’s overall design.
To transport pallets effectively, the MPP range includes modules such as 90-degree transfer units, and rotary turntables with encoders for accurate positioning. New advantages of transfers and turntables include simplifying the design and making installation and commissioning easier and faster. Transfer cars and stacker cranes offer a seamless interface with Interroll’s Dynamic Storage platform taking pallets from production to warehouse storage automatically.
Hilton Campbell, Managing Director of Interroll UK said: “MPP is the ideal solution for any end-user that wants to maximise operational space and efficiency. We’ve listened to feedback and have made improvements to the platform that tick off many of the points on our customers’ wish lists. Our aim is to use the available space more intelligently while minimising transportation times between different areas such as goods receipt, goods issue, storage, production, and picking areas. By automating these processes and simplifying planning, end-users can operate more efficiently.”
Operational and energy efficiency are key drivers behind the 2023 upgrades to the MPP. Energy-efficient DC drives are installed with options for decentralised conveyor systems via the Multicontrol and Pallet Control units. Gravity-powered rollers for dispatch lanes or accumulation conveyors utilise patented Magnetic Speed Controllers (MSCs) that use an eddy current braking system.
Interroll control devices for MPP utilise an analogue interface which enables Interroll’s zero pressure accumulation conveyor technology to be integrated into Industry 4.0 systems. This enhances overall automation functionality, data management, and operational efficiency.
OEMs, system integrators and end-users can benefit from Interroll’s layouter tool that quickly generates 3D layouts to see how the Modular Pallet Platform would work in the space available before ordering components. The tool generates a 3D model of the complete materials handling flow, allowing engineers to tweak the design and alter components to configure the perfect solution. A detailed Excel spreadsheet can be exported that details drives, sensors and specifications of all modules providing controls teams with accurate information to design their control systems.
Once the design has been confirmed, installation of the MPP is simple and straightforward, with the perfectly matched pre-assembled modules fitting together seamlessly. The modular nature of the system also enables easy and cost-efficient changes or upgrades to the material flow system in the future. Due to design simplicity, faster installation and commissioning can be achieved compared to previous versions, saving valuable time on site.
Campbell added: “The upgraded Modular Pallet Platform offers our most flexible solution for pallet handling. Customers can expect seamless material flow, high capacity storage, and enhanced productivity across a wide range of applications.”
Its optimal operating temperature ranges of -28 degrees Celsius to +40 degrees Celsius mean it can be used in a wide variety of warehouse environments, from ambient to deep-freeze environments.