Silo with Automated Pallet Shuttle Storage
15th September 2023
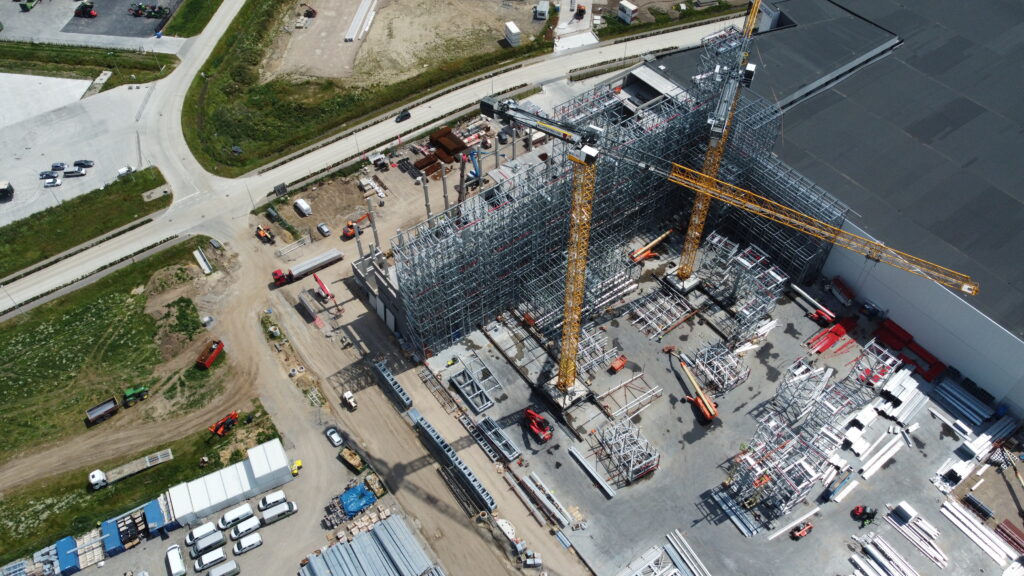
Dematra is a pioneering logistics services company renowned for its commitment to excellence in the industry. Its state-of-the-art, highly advanced 46-meter-tall stow Silo is the result of a highly successful project with the stow Group and demonstrates the future of warehousing and distribution. For this project, unlike most other automated warehouses, Dematra decided to work with shuttles instead of cranes.
The ground-breaking project showcases the pinnacle of automated technology in warehousing: the awe-inspiring 46-meter-tall stow Silo boasts the capacity to house nearly 80,000 pallets effortlessly and is equipped to handle 12,000 pallet movements within a 24-hour timeframe – an international first. Such a level of automation and productivity sets this warehouse apart from conventional counterparts and is set to revolutionise the logistics landscape.
Partnering with the world-renowned stow and the company’s stow Robotics business unit, Dematra has taken warehousing to unprecedented heights with the implementation of the stow Atlas® 2D pallet shuttle system. This cutting-edge automation technology is the backbone of the Silo, ensuring optimal efficiency, speed, and precision in the handling of goods. Dematra specialises in the fast and accurate distribution of various goods within Benelux in addition to operating several modern warehouses, where it manages the entire logistics chain of its customers. This new fully automatic high-bay warehouse on the De Prijkels industrial estate in Nazareth, a town in the Belgian province of East Flanders, cost 50 million Euros.
At the heart of this impressive warehouse are the stow Atlas® 2D shuttles, ingeniously designed to move and organise pallets with unrivaled proficiency. The Atlas® 2D pallet shuttle system consists of a number of Atlas shuttles, the specially designed stow Shuttle-rack system and the local controlling system (STC). The stow Atlas® 2D is a self-powered pallet carrier, which can transport pallets on both the rails of the storage lanes and the rails of the main lanes that run across the storage lanes. The so-called crossings or intersections between the storage lanes and the main lanes are designed for a smooth transition of the stow Atlas® 2D shuttle, either unloaded or loaded.
The automatically controlled shuttles can move pallets horizontally in a fully automatic way and without interfering with each other. The unparalleled flexibility offered by the stow Atlas® 2D shuttles is one of the unique selling points (USPs) of this astounding facility. The dynamic capabilities of the shuttle system means the client can swiftly adapt to the ever-changing logistics requirements of its valued customers, ensuring their goods are efficiently stored and easily accessible.
Meeting the design challenge
Construction of the Silo commenced in early November 2021 and on 1 April this year it officially entered operation. Dematra relied on the knowledge and experience of qualitative and reliable partners that together built this high profile project. The challenge for stow was to be able to deliver a fully scalable, flexible and reactive in-and-out storage system with high throughput, using about 40 Atlas 2D pallet shuttles in a 46 meter Silo.
In designing a compact, extremely stable and flexible in-out storage system with Atlas® 2D shuttles, stow has accomplished two key things: on the one hand the company has built a very large Silo for 80,000 pallet positions that, at 46 metre high, is a significant achievement in itself. In addition, the Silo was built on a very erratic site, resulting in the building an irregular shape rather than a standard rectangle or square building, which means cranes could not be used.
So the second achievement for stow was to install Dematra’s choice of the Atlas® 2D pallet shuttle system for storing and retrieving pallets in deep lanes. Shuttles are much more flexible than cranes, which need a lot of space and are unwieldy.
The Atlas 2D shuttles at heart of the system carry pallets to and from any of the 80,000 storage locations through a total of six main entry points per floor. In this way, the shuttle can change between storage lanes without intervention of an operator or any other means of transportation. There are about 40 shuttles operational here continuously, transporting pallets in large numbers between the front zone of the building and the actual storage area.
These shuttles, which are controlled automatically and can be used 24 hours a day, do no less than 12,000 pallet movements in an 24-hour period – far beyond the capabilities of a conventional warehouse. If there is a lot of work, additional shuttles can be rented if necessary to speed up the throughput even more.
stow is the first, and currently only, company in the world that can manufacture and install this 2D shuttle system. Adding a further unique aspect to the project is the fact that project is the first time stow 2D shuttles are operating in a Silo of this size.
Dematra wanted a very large system that would deliver high density storage of a large number of pallets. Stow’s design was able to accommodate 80,000 pallets on a surface area that is not only relatively very small but one that is also very erratic. Thanks to its height, the building barely takes up 10,000 square meters. Without the height, 5 to 6 hectares would be required, so the ecological footprint is a lot smaller.
Dematra also wanted a very flexible and scaleable system. The throughput of the system is very high due to the number of shuttles that are operational. Throughput can be increased if necessary, simply by adding more shuttles to the system, making it a very flexible system. Finally, Dematra wanted a very reactive system: pallets are only taken out of the system when trucks arrive at the loading dock.
In summary, the key benefits of the stow Silo solution are:
• Proving Dematra with ability to house nearly 80,000 pallets effortlessly
• Providing leading performance, handling 12,000 pallet movements within a 24-hour timeframe, which could not be achieved conventionally
• Providing the required density of storage within a limited compromised footprint
• Providing a system that is flexible and scaleable, allowing adaptation to ever-changing logistics requirements
• Providing a reactive system that moves pallets only when required for greater efficiency
• Provides fast, accurate and efficient handling of goods
Dematra’s 46-meter-tall stow Silo is a true marvel of automation and is set to redefine the concept of warehousing, embracing automation, efficiency, and adaptability like never before. With the stow Atlas® 2D pallet shuttle implementation, this fully automated wonder will undoubtedly set new industry standards, placing Dematra at the forefront of innovation in warehousing and distribution.