Storage Solution for Seifert’s new Logistics Centre
10th November 2020
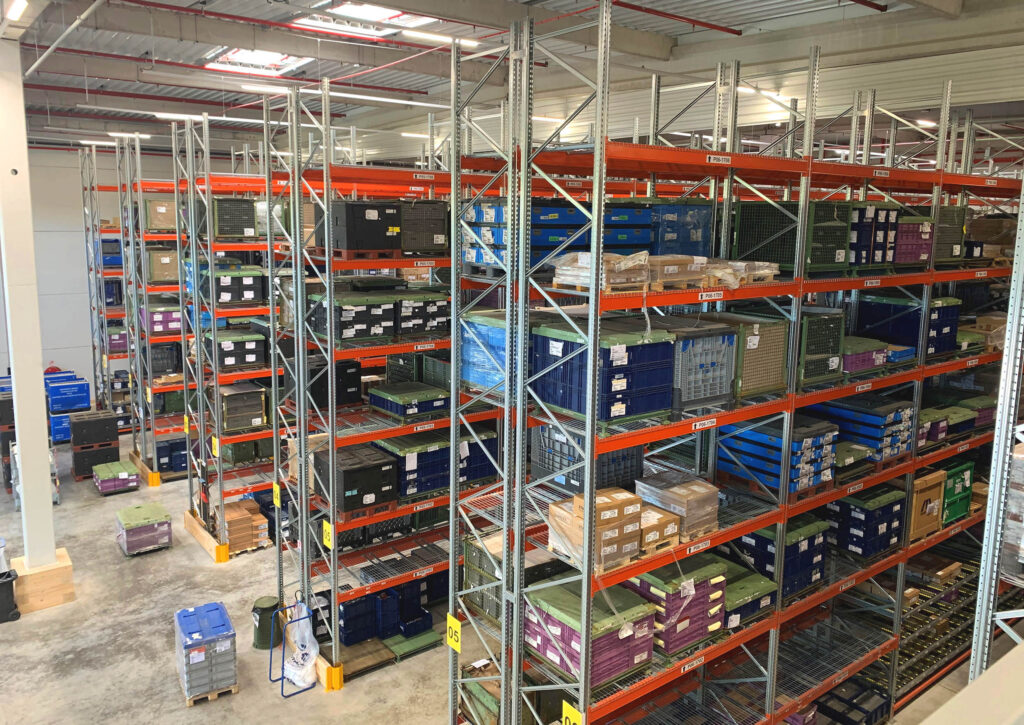
With a precisely tailored racking system for production supply in the automotive sector, AR Racking has created the basis for optimal intralogistic processes in the new logistics center of the Seifert Logistics Group. In addition to the quality aspects, the high flexibility of AR Racking and the fast delivery and assembly time with short time window were important decision criteria for Seifert.
With a turnover of 210 million euros in 2019, the Seifert Logistics Group (SLG) from Ulm is one of the leading freights forwarding and contract logistics companies in Germany. The group is active in Germany, Poland, the Czech Republic and France, and provides warehousing, sequencing, distribution and plant logistics services for well-known customers from the automotive, chemical, pharmaceutical and consumer goods industries as well as the paper and construction materials sectors. The core business of the company is the automotive motive sector. There Seifert is deeply integrated into the value-added chains of the automotive industry. For example, the logistics service provider takes over the production supply for the local Mercedes plants in Rastatt and Leipzig. In Hambach, France, where the Stuttgart carmakers manufacture the Smart, Seifert has been managing plant logistics with around 100 employees on site since 2017. Seifert performs all tasks required for production supply to the automotive plant, from truck registration, trailer yard, goods receipt processing, storage, sequencing and assembly activities to just-in-time and just-in-sequence delivery to the production lines at the Mercedes plant.
Within the Seifert network, the Hambach site symbolizes the increasing internationalization and expansion of the company’s customer portfolio. “On the other hand, the Seifert Logistics Group is thus proving that it is a steadfast and trustworthy logistics partner of Mercedes-Benz AG, which also responds to the needs of the customer on an international level,” emphasizes Luc Wanner, Executive Director Seifert Automotive Logistics. In order to increase capacities at the site and optimize processes, SLG has now set up a new, company-owned logistics center there. AR Racking Deutschland, based in Rüdesheim, was awarded the contract for the design and installation of a racking system tailored precisely to the contract logistics provider’s requirements.
“In cooperation with the purchasing department of our headquarters in Ulm we have received a list of the top suppliers of industrial storage systems“, Executive Director Wanner describes the selection process and the criteria for the award of the contract. “Each supplier on this list was evaluated according to cost, delivery time and quality. In the end, we chose AR Racking. AR Racking offered a very fast delivery and installation time and also helped us in terms of cost when the contract was finalized.”
At the end of last year, the first construction phase of the new logistics center was completed with 20,000 m² and successively put into operation. The second construction phase is to be completed by the end of this year. AR Racking will then install a rack system with a further 4,000 pallet spaces. After completion, the logistics center will comprise a total of more than 41,000 m² of covered area and will be divided into two warehouses with eight units and an office building. “The new building in Hambach was important not only to expand our storage space, but also to be able to react to the rapidly developing requirements of the automotive industry,” explains Wan-ner, “We previously worked in halls provided by our customer, which could only offer sufficient space for his storage needs. The new building has changed everything for us. With the increased storage capacity and the newly acquired independence, we are now able to expand our customer portfolio and target new collaborations.”
The rack system designed by AR Racking offers more than 6,000 pallet spaces. With six support levels, the system in the new logistics hall rises ten meters high. All support levels are equipped with wire mesh floors. Special feature: With a flow rack for small parts storage, an intelligent storage and order-picking solution with 8,600 container spaces was integrated on 41 double bays of the lower rack levels. An additional specification from Seifert was aimed at achieving extensive flexibility in plant layout and logistical processes. “It is fundamentally very important to us to always remain flexible and to be able to react quickly to customer needs,” says the Seifert Executive Director. “Against this background, when awarding the contract for the entire storage system for the newly built hall, we also took care to ensure that the racking system would allow problem-free disassembly and reassembly.”
Within less than four weeks, the intralogistics experts installed the new racking system and completed the first project phase successfully and on schedule. “Thanks to the fully automated manufacturing processes at AR Racking’s production plant, we were once again able to demonstrate our excellent delivery capability with the shortest delivery times in this project with its tight time window,” emphasizes Roland Fischer, Key Account Manager AR Racking Germany. And that despite some previously unplannable constraints. “Right at the start of assembly, it became clear that the free dimensions given to us for route train picking in the racking system were not suitable,” says Fischer. “We had to reschedule the system a little at short notice and, among other things, manufacture, deliver and install other beam lengths. AR Racking was also able to prove that changes and the delivery of corresponding components can be implemented even at short notice.”
Thus, there were no assembly delays in the Seifert logistics center compared to the original schedule. The same applies to additional requirements that Seifert brought in during the project realization. “When we subsequently ordered push-through protections, AR Racking was able to deliver them very quickly and also install them immediately,” Seifert Executive Director Wanner describes an example. “AR Racking’s system guarantees maximum security for our employees and flexibility towards our customers. We are very satisfied with the solution”.
In the meantime, the new system has been completely integrated into the supply of the production lines at the Mercedes plant. “Due to the Corona pandemic, our site unfortunately had to remain closed for a period of 2.5 months,” says Wanner. “This has upset our original schedule. But the planned second phase of the project has now been tackled.” The incoming goods in the new logistics center will be collected after the quality inspection and moved to the storage locations specified by the warehouse management system. Parts and assembly kits are pre-picked and put together according to requirements for the call-off of the demand points in production. The loading of the route trains follows in a sequential order and is made available for transport in the outgoing goods department. “The course of the project from planning to handover of the plant was characterized by good cooperation,” summarizes the Executive Director. If deviations from the original plans occurred, the AR Racking project management always reacted quickly and developed creative solutions to problems. This continues in the After Sales Services. “With AR Racking we have a great partner at our side, who supports us in reacting quickly, flexibly and with quality”, Wanner judges and cites as a current example the announcement from the beginning of July that the main customer Mercedes will sell its plant in Hambach. “There is already a potential buyer,” says the Seifert Executive Director. “This means for us that we will then adapt our processes and the equipment of our logistics center to a new customer. Especially in such difficult times as today, it is a great advantage to have competent partners who are trustworthy and support us in major changes.”