Tips to Boost Warehouse Storage and Handling Efficiency
6th June 2017
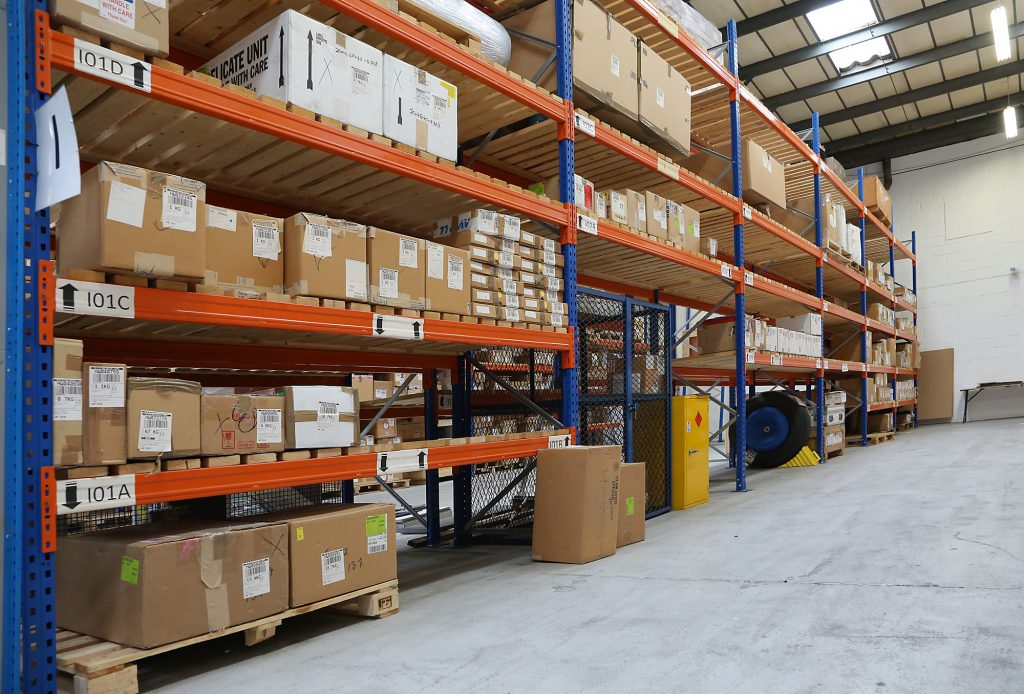
With the supply chain becoming increasingly competitive, businesses want to be more economical, whilst increasing distribution efficiency. Dale Paterson, Managing Director of Exporta Global – Product Handling Solutions FAST, examines the elements needed for best packaging and product handling solutions to amplify productivity and growth.
A warehouse will normally run out of space due to fast development, sizeable discount buying, seasonal peaks, or a slow sales period. To expand storage density, one step is to certify that the facility’s entire vertical cube is effectively utilised. Vertical cube incorporates all space above loads, total building clearance, space above cross aisles, space above work and pick areas.
A formula to check this is to take a sample of unit loads and divide a typical vertical bay of product height by the clear height in that building’s area. If less than 50 percent of the space is employed, prospects for development exist. Create multiple opening heights and execute re-warehousing programs to move slow moving pallets into shorter locations.
A multitude of the right product appears optimistic in terms of order fulfilment and customer service. Yet this can mean you are functioning well below established productivity levels. Alternatively, having too much of the wrong product implies sales projections and production planning were inaccurate. To avoid these issues, leverage outside storage, internal warehouse redesign and enhanced inventory management.
Develop material handling strategies
Improving handling solutions is essential to encourage productivity and reduce costs. Assess the merits of piece picking, where a picker picks one order at a time until the whole order is completed. How cost-effective is this versus batch picking, zone picking or wave picking?
Another tactic is to eradicate handling items twice. Measure and record how many times an item is touched from the time it is ordered until it leaves the building. Fewer touches equals lower costs. Decreasing travel time is vital, as it can account for 50% or more of picking hours. Combining orders into a single distance greatly diminishes travelling time.
You may be contemplating a picking technology such as Radio Frequency, Pick-To-Voice or Pick-To-Light. Such systems can be advantageous as they abolish paper based picking, which may not be cost-efficient.
Boost productivity and security through packaging
Packaging is crucial to any well-run logistics process. By using superior products such as containers, pallets and dunnage, businesses can utilise reusable packaging systems and customers receive orders in mint condition, at minimal cost.
Wasted space in vehicles on return journeys can be counteracted through nestable pallets and collapsible units. These permit companies to stack up to 60 pallets to one stack, rather than 52 pallets. Exporta’s SP1210 range means shipping costs are reduced by up to 15%. Collapsible crates take up less space on return journeys, enhancing the ability for carriers to take more products on board and reducing your courier costs.
Moving to more lightweight solutions, such as plastic reusable containers, these can accomplish substantial lifetime savings. Exporters can benefit from reduced freight costs, as plastics are much lighter than wood and can save as much as £40 per equivalent load bearing pallet.
Decrease losses from theft using rivet-type seals for containers, making them ‘tamper evident’. This enables receivers to instantly see whether the shipment is undamaged and if hazardous materials follow best practice shipping.
To maximise space and advance handling solutions companies should utilise diverse policies, suited to their business model. Merging this with advanced packaging solutions, enables customers to reuse packaging materials, increase the effectiveness of storage facilities and prolong the life of shipped goods.