Ferag and Sparck Collaborate for Automated efulfilment
25th November 2024
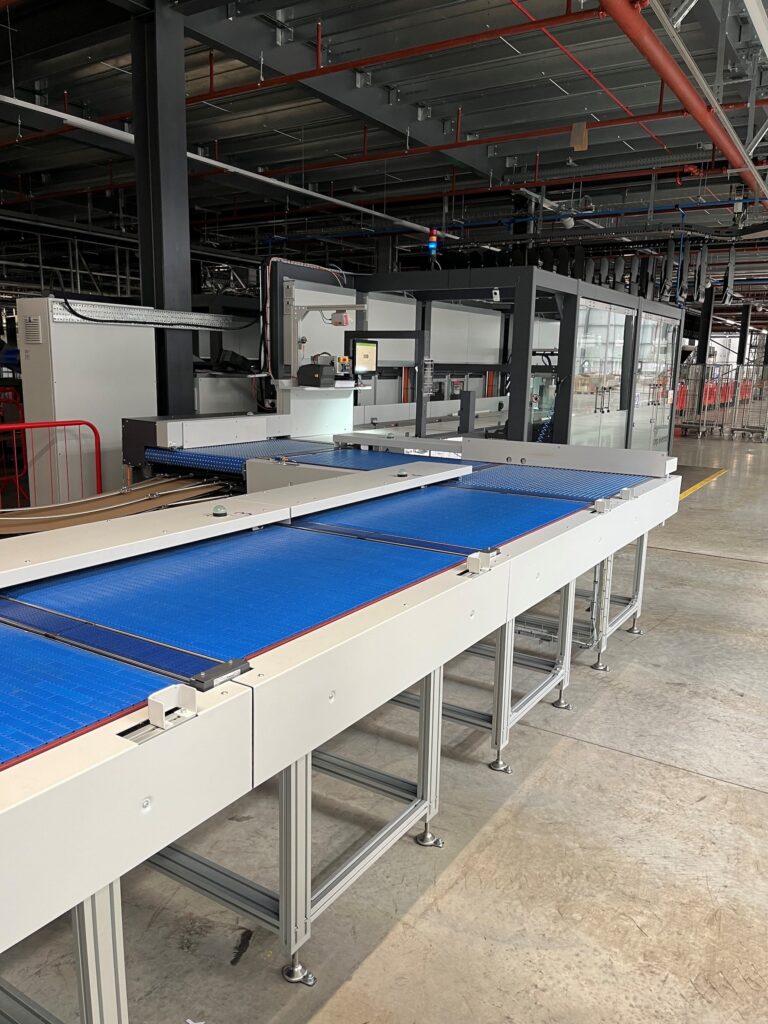
In an ecommerce industry first, systems integrator, Ferag, and auto-boxing specialist, Sparck Technologies, have collaborated to develop a continuous ‘one touch’ process from order-picking to individual ‘fit-to-size’ boxes ready for despatch. The technological leap closes the gap between order-picking and packing, enabling ecommerce businesses to offer its customers secure and compact boxed orders prepared with complete accuracy, and without manual intervention, from pick right through to despatch. A ‘one touch’ operation.
Single system solution
The innovative step, considered a ‘game-changer’, came about soon after Ferag installed its Skyfall automated pouch sortation system at a leading retail brand’s ecommerce centre in the UK. Equipped with 24,000 overhead pouches the Ferag system carries, directs and sorts a wide variety of picked goods from pick-stations, served by ASRS and Autostore systems, to over 70 manual packing benches and one automated ‘fit-to-size’ boxing system – a CVP Everest from Sparck Technologies.
Ferag’s Skyfall pouch system is located on a mezzanine level above the Autostore, maximising the use of available overhead space. Here ordered items are picked from totes into open pouches and carried away, sorted and accumulated within dynamic storage buffers, before being called off to order and delivered at speed to packing benches. The system is designed for a throughput of 16,000 pouches per hour, with a buffer capacity of an hour, where pouches can be held for single or multiple item orders. A key advantage of the system is that each pouch is designed to carry multiple items together – hanging garments, as well as flat-packed and boxed items, such as shoes.
Auto-unloading pouch
The Skyfall overhead pouch sorter was originally sourced to deliver single and multi-item orders to mainly manual packing desks. However, Ferag had recently developed an automated unloading capability for its pouches. This prompted the idea of closing the gap between picking and auto-packing, creating a direct infeed to Sparck’s CVP Everest to automate the whole process. The CVP Everest is capable of producing 1100 boxes per hour with two operators. So, the question was, could Ferag’s pouch sorter and the new Everest boxing system be integrated to produce a continuous process from pick to despatch, with no manual intervention? If so, it would be a game changer.
The challenge
It was a great idea, but it wasn’t without its complications. The highly versatile Ferag pouch sorter is designed to carry a diverse range of goods, making it well suited for varied product profiles, such as garments, accessories, and shoes.
Chris More, Ferag UK’s Head of Sales, explains how the pouch design was critical: “When it came to tendering and specifying the type of pouch needed, we put forward a couple of technologies for consideration, one being our soft pouch and the other being a hard pouch. The hard pouch has a wire frame which allows it to be opened automatically by our newly developed auto-unloading technology. We had various options for unloading, and a gentle unloader was ultimately selected. This would prove critical.”
But the challenge was, how to present a wide variety of products with different profiles in the right order and orientation to Sparck’s CVP Everest? It was a complex issue.
As it happens, Sparck Technologies’ development team was in the process of looking at ways of auto-infeeding items, as singles and possibly multiple units, into their automated boxing machines to remove the need for manual intervention. The CVP machines had always required manual induction of order-items for an otherwise completely automated process of 3D scan, cut-to-size, fold, seal and label, and then on to despatch.
“We immediately knew we could provide a solution as we were already working on a more holistic approach to the problem, with agnostic, scaleable and modular solutions,” said Jo Bradley, Business Development Manager for Sparck Technologies in the UK.
More added, “We understood exactly what was needed, so we entered into close collaboration with Sparck to set out how the two systems would exchange information, creating a tight integration between upstream and downstream processes, with reliable hand-over and acknowledgement of product and order information.”
Meanwhile, Sparck carried out further work related to ensuring a smooth and consistent induction of a variety of sized items to the CVP Everest. A clever ‘Z’ shaped conveyor section efficiently aligns and positions each item ready for 3D scanning and processing, providing a well matched, consistent pace sequenced with the upstream Ferag sorter.
Counting the benefits
After thorough testing in late summer 2023, the ‘one touch’ solution went live. The performance of the system has exceeded the retailer’s expectations, with accurate, consistent and reliable delivery of ‘right-sized’ boxes to despatch, maximising the full potential throughput of the system and standing as testament to the successful collaboration between Ferag and Sparck.
Bradley says: “Automating the interface between order-picking and ‘fit-to-size’ boxing has been a ‘Holy Grail’ for the sector for a number of years. Creating a smooth, seamless process free from human intervention has not been easy, given the complexity of the task, but now we have developed technology that aligns and positions individual items for induction into our CVP machines with great speed and accuracy. We are delighted to have worked with Ferag on achieving an industry first.”
With no need for direct human intervention between upstream order-picking processes and the fast, automatic production of ‘right-size’ ecommerce boxes – cut, formed sealed and labelled, ready for dispatch – exposure to risks, such as labour shortages and sickness, are significantly reduced. Flexibility to ramp up easily for peaks is an added bonus. This innovative step takes out cost, increases throughput and offers the retail client the reassurances they need to perform efficiently at peak.
similar news