Packaging: KHS Launches Modular Labelling Series
7th July 2020
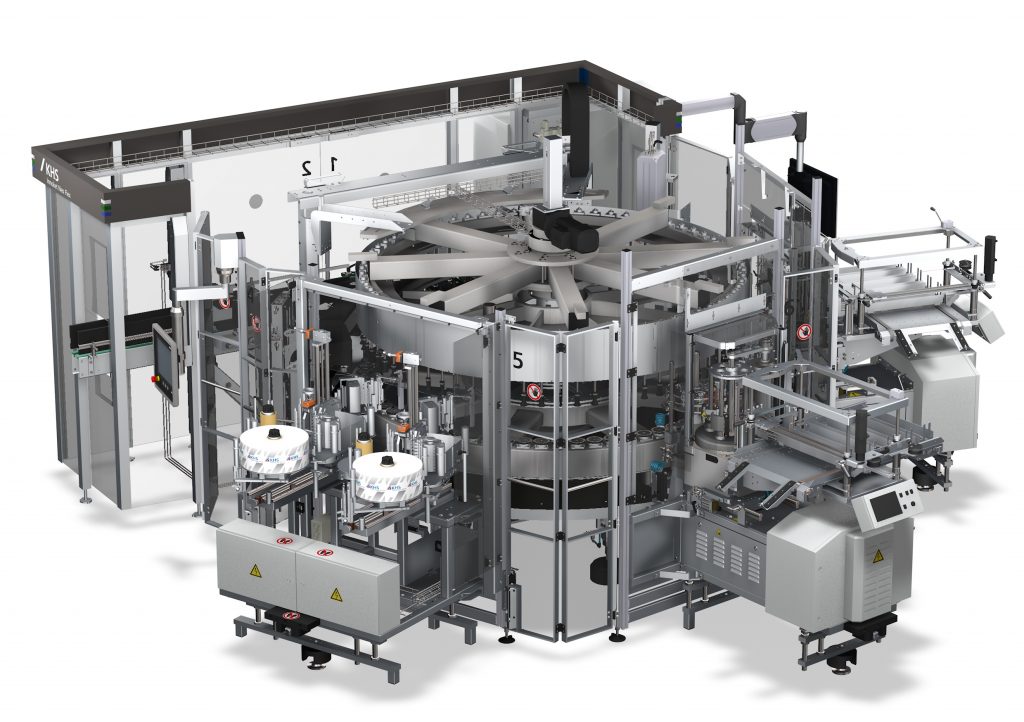
Filling and packaging specialist KHS is launching a new modular labelling product. The KHS Innoket Neo Flex and KHS Innoket Neo series replace the previous Innoket SE generation of machines.
Thanks to the Innoket Neo’s flexible design the individual modules on this highly customizable labeller can be freely combined, says the company. Henrik Kahrmann, who works in Product Support at KHS, outlines the benefits. “In the past there was a separate machine for each different labelling technique. This was optimized for its specific area of application but reached its limits when customers wanted to expand their portfolio, for example by adding self-adhesive labelling in combination with the classic cold glue method.”
With the Innoket Neo KHS has developed a machine that can be configured at will thanks to its modular design. The new Innoket Neo Flex goes several steps further when it comes to standardization and meets all customer demands in a single series – regardless of whether with permanently installed stations or as a modular machine. Depending on the machine size and respective requirements the Flex series can be equipped with two to four modules. These are exchanged with just a few manual adjustments performed without tools.
Labeller convincing with its wide range of application
The Innoket Neo Flex also demonstrates great flexibility in the choice and size of container. The machine labels both plastic and glass containers and cans in all of the standard sizes. The output totals up to 74,000 containers per hour. Depending on requirements all further standard capacity ranges can also be catered for.
The flexible Innoket Neo Flex can be used as either a single machine or as part of a production line. “Our labellers have been designed so that they can be easily integrated into any existing or planned line,” says Kahrmann.
Low maintenance and ease of operation
Another advantage of the new modular machine is its extreme ease of operation. With its patented folding door technology the machine carousel and individual stations are readily accessible at all times. Moreover, no additional cladding is required for the area beneath the machine table. In addition, operators profit from bearings lubricated for life that make the labeller extremely low maintenance and reduce the amount of lubricant needed. The new, ergonomic HMI provides great ease of operation. This can be moved by the operator to the required position very simply.
The Innoket Neo Flex is equipped with future-proof TIA[1] technology from Siemens. “The combination of TIA Portal and SIMATIC S7-1500 controller results in significant performance benefits in the control unit’s reaction time,” Kahrmann explains. The labelling machine also has a simplified electronics concept, in which most of the components are installed in the control cabinet. The perfect combination of central and decentralized control calls for much less cabling.
Fast supply of spare parts and consumables
Parallel to the standardization of its machine series KHS has also significantly speeded up the supply of spare parts to its customers. At the same time the supply for all existing machines continues to be ensured without limitation. For optimum operational behavior and low wear KHS provides all of the necessary consumables such as glue and also advises its customers on materials that are difficult to process at its own label laboratory – especially set up for this purpose.
[1] TIA = Totally Integrated Automation.