4 Steps to a Sustainable Transport Packaging Solution
10th October 2024
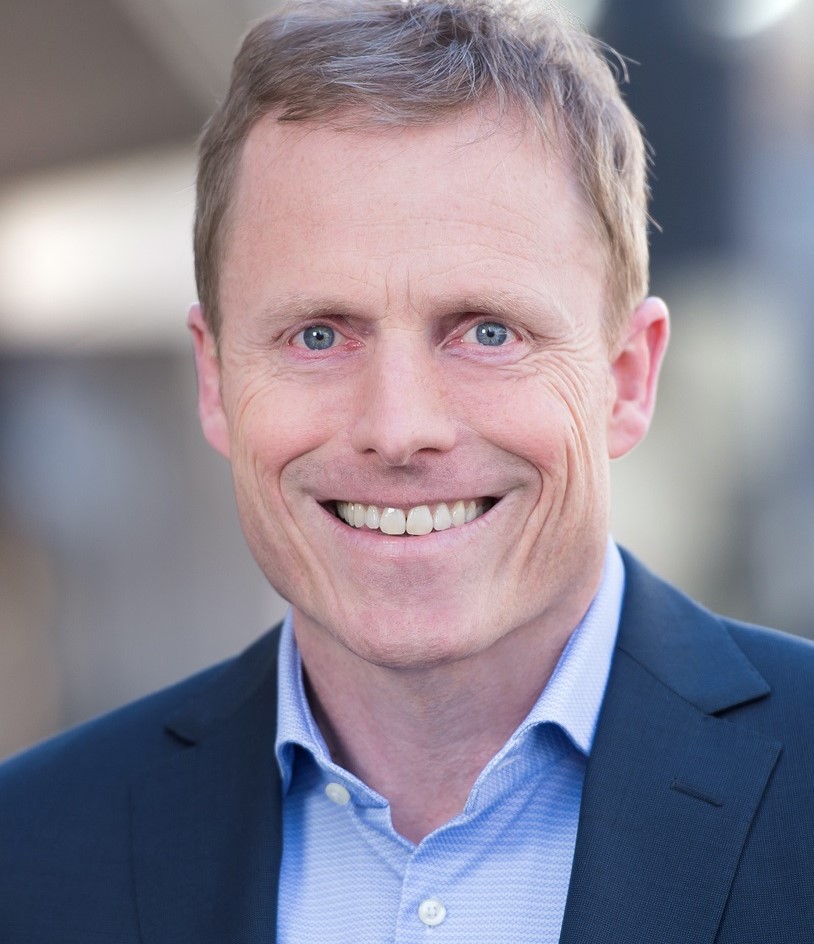
In order to make their supply chains more resilient, companies invested more in sustainability in 2023. According to a global survey of 600 supply chain management executives conducted by Blue Yonder, almost half of the participants (48 percent) invested capital in this area. “New pressure is also coming from legal regulations such as the European Packaging Regulation which requires sustainable and recyclable packaging,” says Jürgen Krahé (pictured), Senior Commercial Director EMEA at ORBIS Europe. “Companies have many options for making their logistics processes greener. Switching to sustainable transport packaging is one of them.”
Under the right conditions, reusable plastic containers can help to make supply chains more environmentally friendly. With a service life of over ten years and a high proportion of recycled material, they reduce resource consumption and the need for new transport solutions. These four steps should be followed when making a switch:
1. Analysis of the supply chain
The first step is to assess whether it makes sense to switch to reusable plastic packaging for your own application. Using software-based life cycle assessments, companies can determine the environmental impact of different types of packaging over their entire life cycle – from raw material extraction to production, transport and use to disposal. Based on information on transport routes and means, the Packaging Lifecycle Assessment Tool from ORBIS analyses whether CO2 emissions, energy and water consumption and waste can be reduced by switching to plastic packaging. “Only when the environmental impacts have been translated into concrete figures can companies make well-founded investment decisions,” says Krahé.
2. Concept development and success measurement
Once all the requirements are known, companies need a concept to integrate the new transport solution into the existing supply chain. To switch to plastic, they must first determine whether a customized solution is required or whether a standard product is sufficient. Then they have to decide: Is a test phase with prototypes required and, if so, for how long? Should the solution be rolled out completely or in stages?
What legal requirements must be observed with regard to transport and storage (for example in terms of fire protection concept)? Suitable key performance indicators help to make added value such as cost savings, reduced CO2 emissions or energy consumption measurable.
3. Implementation and optimization
During the roll-out phase, feedback from customers and suppliers is incorporated into the optimization process. If companies then implement the finished transport box throughout the supply chain, the solution must be continuously adapted to changing circumstances: For example, if there is a new production process, a new work procedure or the company is introducing another product with a new design or size, it must be checked how this affects the transport packaging and what adjustments may be necessary.
4. Disposal/buyback
At the end of their lifespan, plastic packaging can be recycled up to 100 percent and reused for new packaging. This reduces greenhouse gas emissions and conserves valuable natural resources. In addition, companies can offset the initial higher costs and save disposal costs. “So that companies don’t have to deal with this themselves, ORBIS Europe buys back obsolete or irreparably damaged plastic packaging at the material price,” says Krahé. “In this way, the organizations contribute to an almost closed raw material cycle and benefit from economic advantages.”
Reusable plastic packaging represents an ecological and economical alternative to materials such as wood, steel or cardboard. They can help to meet legal requirements and the increasing sustainability expectations of other stakeholders.
similar news
Packager’s Online Sustainability Hub Highlights Plastic Positives