“50% Productivity Boost” at Automated Pallet Repair and Service Centre
24th October 2017
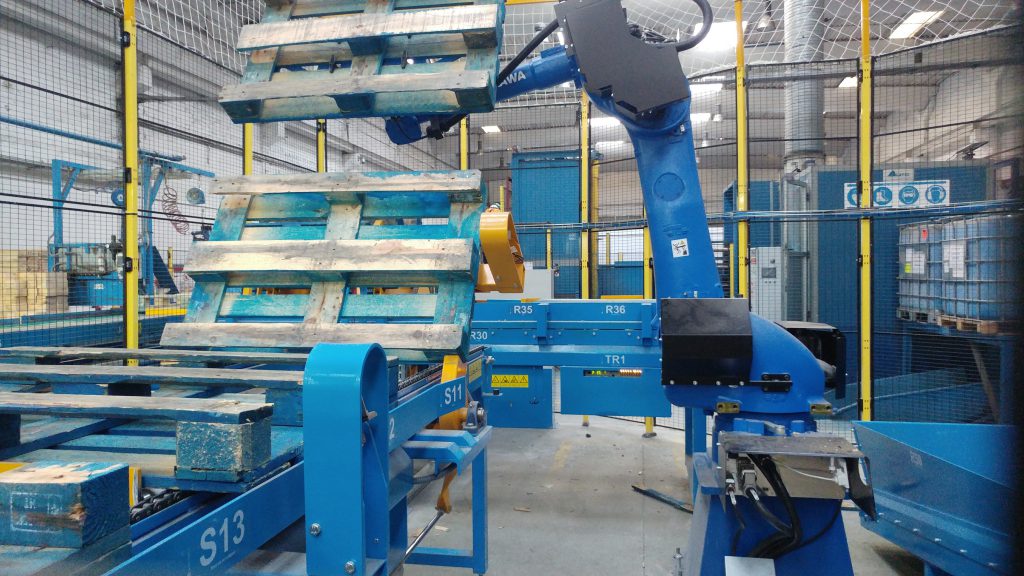
CHEP UK & Ireland has opened a new state-of-the-art pallet repair and service centre facility in South Ockendon, near Thurrock, Essex (UK). The new facility stands on the existing CHEP site and delivers increased availability for the growing pallet demand from customers in the South-East region.
CHEP has invested more than £2 million in equipping the facility with some of the most advanced automatic fault-detection and repair equipment available. In response to the rapidly evolving needs of its extensive customer base, the new automation equipment will deliver significant efficiency and productivity improvements. This investment in automation will enable a higher level of consistency in pallet quality with the added benefit of improved levels of platform consistency and appearance for all customers.
CHEP UK & Ireland, Vice-President and Country General Manager, Helen Lane, said: “The key areas where the automation will deliver these productivity and efficiency improvements are inspection, repair and paint stencilling. Customers will benefit from improved levels of platform consistency delivered by this increased automation and reduced manual intervention required in the conventional inspect and repair process. Additionally, the South Ockendon site is in the ideal location to effectively manage the large number of satellite pallet processing operations installed for customers on their sites in the South of England.”
The newly-installed automated equipment includes:
> The latest laser system that checks individual pallets for damage, and works in conjunction with an automatic cutter to identify and remove any broken elements.
> A robotic arm lifts the pallet and based on information provided by the Automatic Digital Inspection system (ADI), cuts and removes the element to be replaced then returns the pallet to the repair bench where the operator completes the operation.
> The latest roller nailer technology guarantees no nails protrude more than 3mm above the top board of any pallets.
> Moisture content of pallets can also be monitored thanks to technology which probes the top deck of pallets. If the moisture content exceeds a certain level, the pallet will be removed from production.
As a result of this automation, it is expected that the new facility will be 50% more productive than previously, with the ability to process approximately 6.2 million pallets per year, compared with 4.1 million pallets at the original facility. Both B1210A standard and B1208A Euro pallets will be handled, with the flexibility to switch products in response to changes in customer demand. Staffing at the new facility will remain the same as previously with approximately 85 full-time CHEP employees.