CSR Commitment in Q-Pall’s New Netherlands HQ
24th July 2019
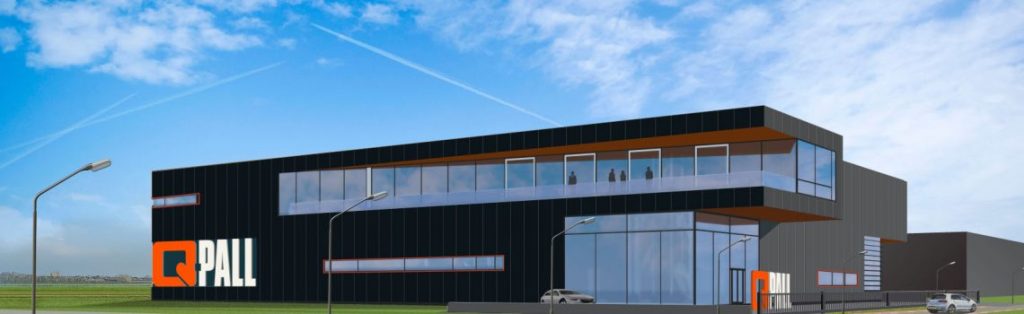
The construction of European plastic pallet specialist Q-Pall’s new Netherlands headquarters has begun. The new location in Veghel along the A50 and is expected to be complete by the end of this year. The new building will house both the new European headquarters and a new industrial hall and will further expand this company, which was founded in 2005, and also offers good opportunities for Corporate Social Responsibility (CSR), which is especially important to Q-Pall.
Q-Pall’s commitment to CSR is shown by the design and the construction of the new headquarters and the new industrial hall. Foundation piles were already present at the building site, which were taken into account in the design of the location. This not only saves on construction costs, but also prevents unnecessary use of materials. In addition, the new construction enables Q-Pall to take other major steps in the field of CSR. For instance, an air/heat pump and solar collectors will not be missing on the roof, and the new building will be virtually energy-neutral.
The design of the building is sleep and simple, but due to large windows, large overhangs and the integration of things like the awning into the facade, it will be a beautiful building. It is the next and large step in Q-Pall’s desire to produce sustainable plastic pallets in an efficient way.
Q-Pall is a major European player in the field of manufacturing plastic packaging materials, particularly plastic pallets. What is characteristic is that Q-Pall has the production of plastic pallets take place on the location where there is a need for those pallets as much as possible. This is achieved by transporting the moulds that are used to create the pallets to the local production facility. Transporting only those moulds results in enormous savings on transport kilometres, and therefore, on CO2 emissions and the costs of trucks.
A concrete example: if plastic pallets are produced in the Netherlands that are intended for the French market, this means many full trucks need to make long trips to the south and back. By only transporting the mould to France and producing the pallets locally, huge savings are achieved in terms of transport kilometres and, as a result, the CO2 emissions. There are currently production locations in Balk (NL), Ringe and Marktoberdorf (D), Ribe (DK) and Nantes (F).