Auto Parts Packaging Automation
30th December 2020
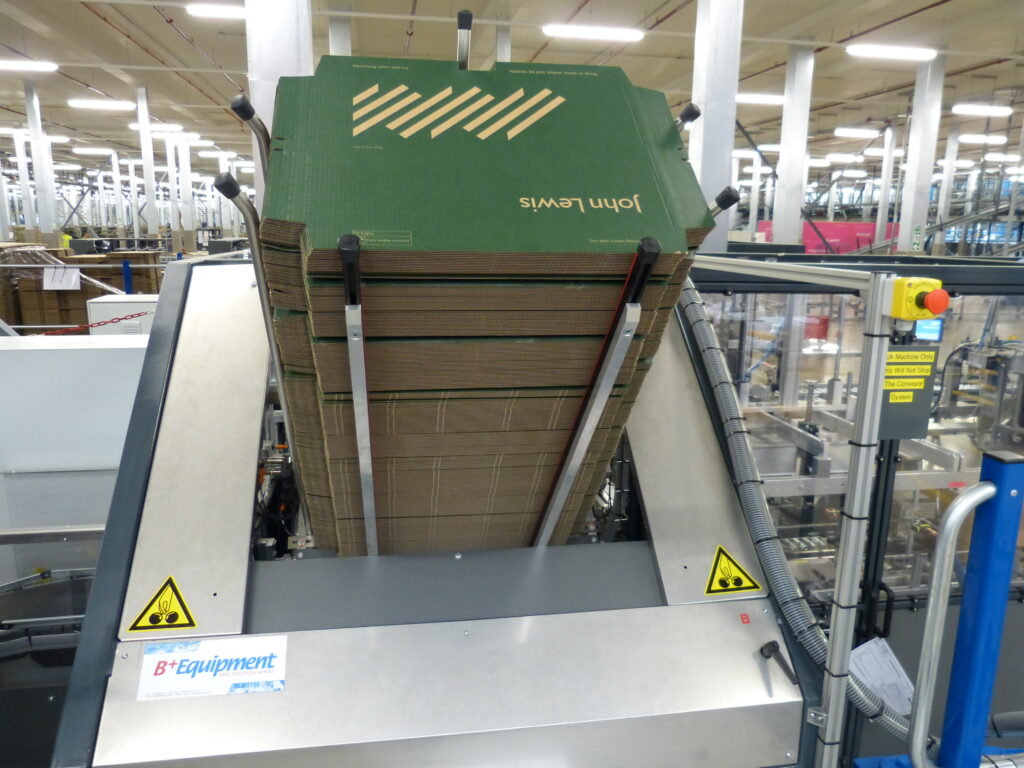
An automated packaging system has the versatility to deal with fragile and heavy automotive parts of many shapes and sizes, reports Paul Hamblin.
Founded in 2001 as an eBay shop for auto parts, kfzteile24 is now Germany’s leading multi-channel supplier for vehicle parts and accessories. The company operates leading online shops in five countries as well as a total of three specialist car markets with associated master workshops. An efficient call centre rounds off the comprehensive service available to the customer. More than
one million customers per year, from professional mechanics to workshops and end users, trust kfzteile24.
The range of more than one million items is sent from the Berlin logistics centres, which employ over 500 people. In 2012, when the daily order volume was around 2000, kfzeile24 decided that, due to continued growth, a major investment project in its logistics was required. The first step was the construction of a distribution centre to replace several small warehouses. Initially order picking operations remained manual, then an automation project was launched in 2018 to prepare the company for continued strong growth.
kfzteile24 first met B+ Equipment at an exhibition in 2012. The aim was to get to know the available solutions and to evaluate their compatibility with car parts. B+ Equipment began by carrying
out a formal study showing that the multiple methods used by the auto parts supplier for its manual processes could be advantageously replaced with just two formats, plus a packaging solution offering height reduction. B+ Equipment recommended its I-Pack solution, which consists of forming a tray, placing products inside, and finally reducing and closing the box. For the entire project, including the ramp-up, kfzteile24 called upon the expertise of consultants Vialog.
With a high rate of multiple orders, kfzteile24 considered that the I-Pack solution offered a guarantee of reliability for numerous heterogeneous orders with unstable products. “We decided to choose the machines from B+ because we had to increase shipping performance thanks to good business development,” explains Marco Hermann, Head of Logistics at kfzteile24. “It was also important for us to optimize visual presentation of the delivered packages to our customers and to reduce physical strain on our employees.”
The packaging specialist’s pedigree was another factor. “B+ offers decades of experience in the field of automated packaging,” Marco Hermann goes on. “We were impressed by the solid
technology and simple functional logic of the systems. In particular, the height reduction via folding has a big impact on the stability of the package. A simple technical & IT interface was also important for kfzteile24. B+ offers here a very smart and easy solution,” he sums up.
Packaging system and product protection
In 2019, B+ supplied two tray erectors and two I-Pack machines that are integrated into an automated packing line from which the boxes are directly transported to the user. The Packing Lines are integrated in the Order Consolidation Areas. This setup enables high performance and fast dispatch of customer orders. As car parts can be fragile and/or very dense, and also come in many
shapes, not to mention being expensive and highly valued by the customer, most boxes require reliable product cushioning. kfzteile24 has opted for a creased paper cushioning system that operators place by hand at the same time as the products in the gaps. Here too, the I-Pack solution is perfectly compatible with this cushioning solution.
The automated system has been in operation since March 2020 and is sending about 13,000 parcels a day, up to 80% of all company orders, via its transport service partners. Marco Hermann is very pleased with the results. “Working with B+, we have experienced professional and reliable sales teams, goal-oriented project management and customer-oriented solutions. For us these factors are elementary components for a good partnership.”