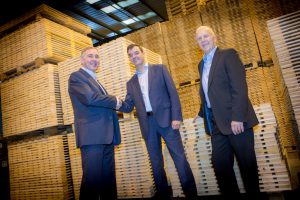
Scott Group has acquired Cheshire-based Northern Case in a strategic deal which supports Scott… Read more »
Scott Group has acquired Cheshire-based Northern Case in a strategic deal which supports Scott… Read more »
One of the largest manufacturers of snack foods in the UK has celebrated 10… Read more »
Inka says its disposable pallet is the ideal cargo carrier for air freight: low-cost,… Read more »
Goplasticpallets.com and Goplasticboxes.com will be returning to IMHX 2016 at the NEC in Birmingham,… Read more »
Dutch start-up company Ahrma launches a revolutionary pallet at the K-Messe in Düsseldorf. Ahrma… Read more »
Palletways, Europes largest provider of express palletised distribution services, has announced that Imperial Holdings… Read more »
Increasing focus on the disturbing noise in everyday life, allied to extended shop opening… Read more »
Greater Manchester-based haulage company Express Parcel Services (EPS) has become the latest organisation to… Read more »
UK-based independent supplier of plastic pallets Goplasticpallets.com has introduced the first of a new… Read more »
European pallet pooling provider, LPR, has opened two new depots in Ireland. Building on… Read more »
SSI Schaefer has delivered a new pallet storage solution to Yearsley Logistics Belle Eau… Read more »
The new SF 800 H Retail Pallet is the latest model to join Goplasticpallets.coms… Read more »
The first shipment of pallets has arrived at the new Isle of Harris Distillery… Read more »
2015 marked the eleventh successive year of double-digit growth for IPP Logipal UK &… Read more »
Qimarox has brought to market its Prorunner mk10 product elevator. Based on the design… Read more »
Goplasticpallets.com has introduced a new lightweight collapsible pallet box to its range, which it… Read more »
Zupplychain, a brand new b2b website to match warehouse space with pallets needing storage,… Read more »
Q-Pall has introduced the first of a new line of improved plastic pallets, claiming… Read more »
At LogiMAT (Hall 3 / Stand B31), Cabka IPS will be showing selected products… Read more »
The new Hyster® RP2.0-2.5N series has been designed and built for intense use in… Read more »
The new appointment of Tom Lee as Project Sales Manager marks a period of… Read more »
Crown, one of the worlds largest material handling companies, further expands its European warehouse… Read more »
Wiltshire-based logistics company UK Shuttle has started its dramatic growth trajectory by becoming the… Read more »
Combining the key benefits of platform and seated models, the Yale MPT series rider… Read more »