More Throughput for Coop DC During Upgrade
15th September 2023
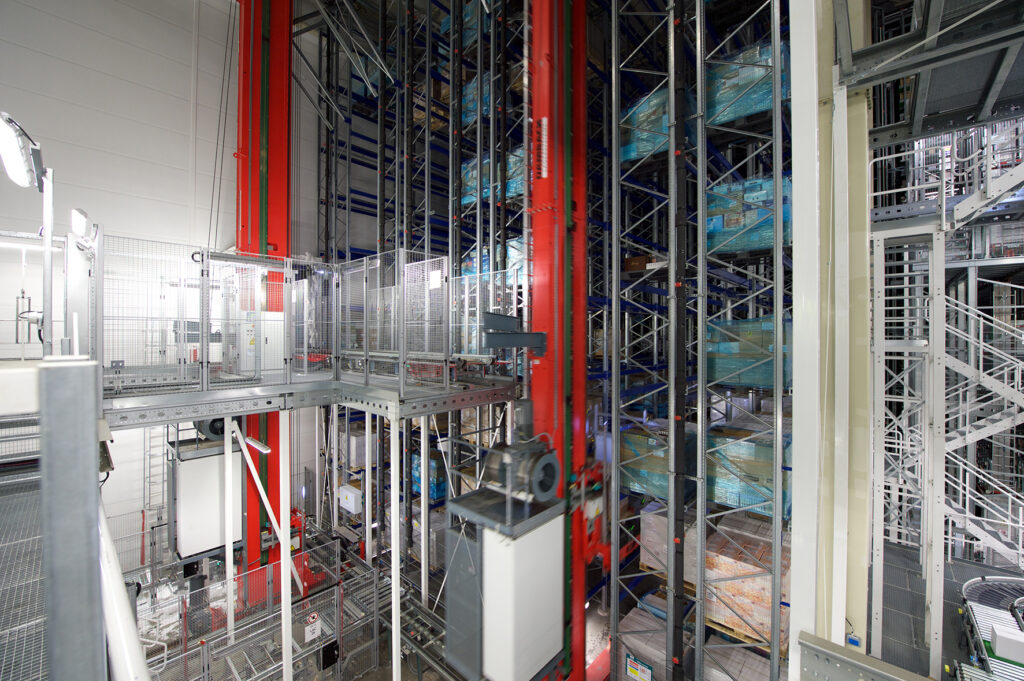
Expanding a highly dynamic multi-temperature logistics centre for roughly 1,200 stores during ongoing operations with an increase in pick performance from 480,000 to almost 625,000 cases daily, is a tremendous challenge as such. But when, in addition, store and online orders continue to soar due to various lockdowns and the teams are only allowed to work with severe limitations because of Covid 19 restrictions, then a lot more than just technical and organizational knowledge is needed on both sides for the project to succeed. WITRON and the food retailer COOP from Norway have demonstrated this impressively.
When the two managing directors Geir Inge Stokke (COOP) and Helmut Prieschenk (WITRON) signed the contract for the expansion of the COOP multi-temperature distribution centre near Oslo at the end of May 2019, neither of them had any idea of the huge challenges they would have to face. From March 2020, the world stood still due to Covid, and the consumers’ demands significantly soared driven by various lockdowns. This was an inauspicious start for what was probably the most challenging brownfield project in WITRON’s company history to date, in which existing technology was modernized and new modules integrated – both in the existing building and in a new extension facility.
The task addressed to Gaute Glomlien from COOP and Holger Weiß from WITRON was described as follows: to expand the dry, fresh, and frozen goods logistics facility from 52,000 square meters to 84,000 square meters under Covid 19 safety measures, to increase throughput by 30 percent, to integrate new COM machines, to install additional pallet and tray AS/RS aisles and various conveyor components, to increase the size of the fully automated shipping buffer, to update the corresponding WMS system to the latest technology, and to implement all of this into the existing material flow during ongoing operations without any loss of performance.
“We were able to save millions of euros yearly in the past with the WITRON systems. Therefore, it was clear that we would also realize the expansion with WITRON and their leading logistics technology”, explained COOP project manager Glomlien. The expansion was also necessary because the retailer acquired a competitor and therefore grew stronger and faster than assumed when the logistics centre was established.
“COOP is a showcase project for us. Many international customers visit the facility and with the expansion we were able to impressively prove that we can handle such a task during ongoing operations on budget and on time despite increasing volumes – both in terms of throughput and items – in the warehouse and despite the pandemic”, Holger Weiß proudly reports. In spring 2023, 42 COM machines (eleven new COMs were installed) will be operating across all temperature zones and COOP’s logistics systems can pick more than 625,000 cases daily. In total, the facility comprises more than 600,000 pallet, tote, and tray storage locations as well as 130 stacker cranes, and many kms of conveyor technology.
Challenges successfully mastered
From the facility (with five different temperature zones), COOP supplies 1,200 stores located across Norway, from the metropolis region around Oslo and the far North of Norway from an assortment of 13,000 different items. “At the beginning of the project, it was evident that we needed to increase our pick capacity substantially”, Glomlien jokes today. “The volume of the logistics center has almost doubled”, Weiß responds laughing. Glomlien and he have had tough discussions in some situations. Today, they sit in front of the Teams microphones and are happy to see each other again virtually. “It was a good time”, summarizes Weiß after the conversation, and his Norwegian counterpart agrees.
When he recalls various days, weeks, and months in the project, he pauses for a moment, recalls, and then continues all the more proudly. “The borders were closed. There had been complex entry restrictions. The authorities ordered strict quarantine measures. For a long time, the project team was only allowed to drive from the hotel (which was not allowed to be left for other reasons) to the logistics center and back. The cafeterias on site were also closed. Even in the hotel, the service was reduced to a minimum. This is something you have to overcome as a team. These are real deprivations – for the customer team, but also for our colleagues. As a project manager, you ask yourself every evening how you can keep your team motivated”, emphasizes Weiß. The WITRON team moved around with special permits from the government. COOP’s logistics was systematically important. “During the pandemic, the number of orders increased even further”, Glomlien recalls.
The frozen food logistics sector was a particular technical challenge for the Upper Palatinate Holger Weiß. “We “heated” the existing automated area from minus 25 °C to minus 5 °C, and COOP temporarily moved the goods to a conventional storage area for picking. Within eight weeks, we then made all the adjustments in the area of electrical assembly, platforms, pallet and tray conveyor technology until the existing freezer was ramped up again. The two new COM machines, as well as two more pallet storage aisles, four tray storage aisles, additional stacker cranes, a de-palletizer, and the corresponding conveyor system were then installed in the new freezer building.
“The installation sequence was carefully planned in a joint process, and we prioritized installation of the new pallet cranes first, which would facilitate efficient CPS picking in the extended frozen area. We then cooled the new production zone to the required temperature, moved our automated production to CPS picking from the new pallet cranes and manual pallet racks, and heated our existing production area to accommodate WITRON’s installation“, Glomlien adds. “The phase required careful coordination and cross-functional collaboration between WITRON’s IT and mechanical resources, and COOP’s teams controlling production, transport and order management, from commissioning through ramp-up and during the productive phase.
After WITRON had completed the new installations in our pre-existing production zone, the process was reversed for completion of the new production area. Picking was then moved back to the fully automated OPM machinery.”
At COOP, those responsible also refer to the picking area as the production area, explains Holger Weiß.
Today, a total of four COM machines are working in the frozen goods area of the facility. When the system was cooled down again to minus 25 °C, Weiß crossed his fingers. “If the cables break, the belts tear, motors quit, or sensors fail, it’s going to be exciting because the available time window was tight” and at the same time it was important to keep in mind the quality of the stored goods to avoid major product damages. “You have to use the best components available on the market for a project like this. We did not change existing drives, but we installed new ones. It has to run right from the start, because otherwise the project won’t be completed on time, or the customer will even have direct costs if goods cannot be shipped.” The WITRON OnSite team used the time of the rebuild to perform maintenance on the system. “When the goods are stored again, you must always constantly communicate with the control room and react quickly on site”, explains Weiß. Communication between the customer team, the project team, and the OnSite team must work smoothly. “The result undoubtedly documents that it worked smoothly”, emphasizes the WITRON project manager. “The meticulously detail work paid off. After we had ramped up the frozen goods area, we were able to quickly return to performance. There were no negative surprises.”
Efficient modification concept also for the dry goods range
Following detailed discussions with WITRON, COOP decided to install five additional COM machines (a total of 17 with space for 4 more COMs), another four pallet storage aisles, ten more tray storage aisles, the corresponding stacker cranes and conveyor system mechanics, three depalletizers, as well as one stretch-wrapper in the OPM area of the dry goods range. “A crucial phase had come for the dry goods range in the fall of 2021 and winter of 2022”, says Glomlien. “This is the area with the highest throughput in the distribution center, with added complexity with two physically separate OPM sub-systems working as one integrated unit. In order to continue supplying all orders on time with the same quality after start of use of the new area, the ramp-up process was planned carefully, and our stock distribution was monitored closely to ensure the right products were in position for picking at the right time”, says Gaute Glomlien, describing the well-planned expansion. ”Detailed emulations performed upfront by WITRON’s IT team, in collaboration with COOP’s production leaders, were also crucial to identify the correct production strategy prior to start of use of the two fully integrated sub-systems “The decisive factor here is the exact balancing of orders and inventories between the individual sub-systems”, adds Holger Weiß. “This implementation strategy has also worked excellently.”
Optimizing picking strategies
The fresh food area received four additional COM machines (in total 21 with space for five more COMs), another eight tray storage aisles, two more pallet storage aisles, the corresponding stacker cranes and conveyor system mechanics, two de-palletizers, and one stretch-wrapper. “We then added another material flow section for vegetables and fruits in the fresh produce area to simplify the handling of other goods in this sector. In the past, the product groups were picked together”, explains Glomlien.
The fully automated shipping buffer, which covers various temperature zones, has been expanded once again.
Holger Weiß is already working on his next project in Sweden. Day-to-day business continues for COOP at CLog. “The upgrade has given us a state-of-the-art solution that has been enhanced during ongoing operations to a throughput volume that could not even have been anticipated in the original design phase. Now, we are further optimizing the processes”, explains Glomlien. With the expansion, also COOP’s software systems were updated to WITRON’s state of the art.
But even after the project has been completed, the processes in the logistics centre keep changing, if only because the entire supply chain is subject to fluctuations and customer requirements change. That is why a high level of flexibility is required in all processes. “COOP is pursuing a continuous improvement process and has gained a lot of experience with the facility over the past few years. This is also very impressive for us. They analyse their data, their calculations, select the right picking strategies for the regions and stores, and define how to structure their orders”, says Weiß enthusiastically. They also support the WITRON colleagues on site and in Parkstein when logics change.
Respect extends to all parties involved in the project
Also for WITRON CEO Helmut Prieschenk, the facility in Norway is a showcase project in many aspects. “It shows the transformability of automated processes. It shows how efficiently additional technology can be integrated into an existing system or into an existing building during ongoing operations. However, it is not only technology and buildings that are decisive in such projects, but also the people who successfully carry such a project across the finish line. People who have shown how even challenging situations can be mastered efficiently when project teams cooperate in a constructive and trustful manner throughout all project phases.
With this expansion, all those involved in the project have delivered a masterpiece. Both technologically, but even more so in terms of the commitment shown. While the technical requirements were already a challenging task for the COOP and WITRON teams, their implementation was further complicated over many months by the Corona pandemic. In order to meet the necessary tight time schedule despite health policy impairments, the colleagues showed a maximum of “heart and soul”, grew with the challenges, and did a great job. Projects are made by people for people. And the people involved have delivered a performance that deserves the utmost respect and represents the spirit of both companies.”