Quick and safe
15th December 2015
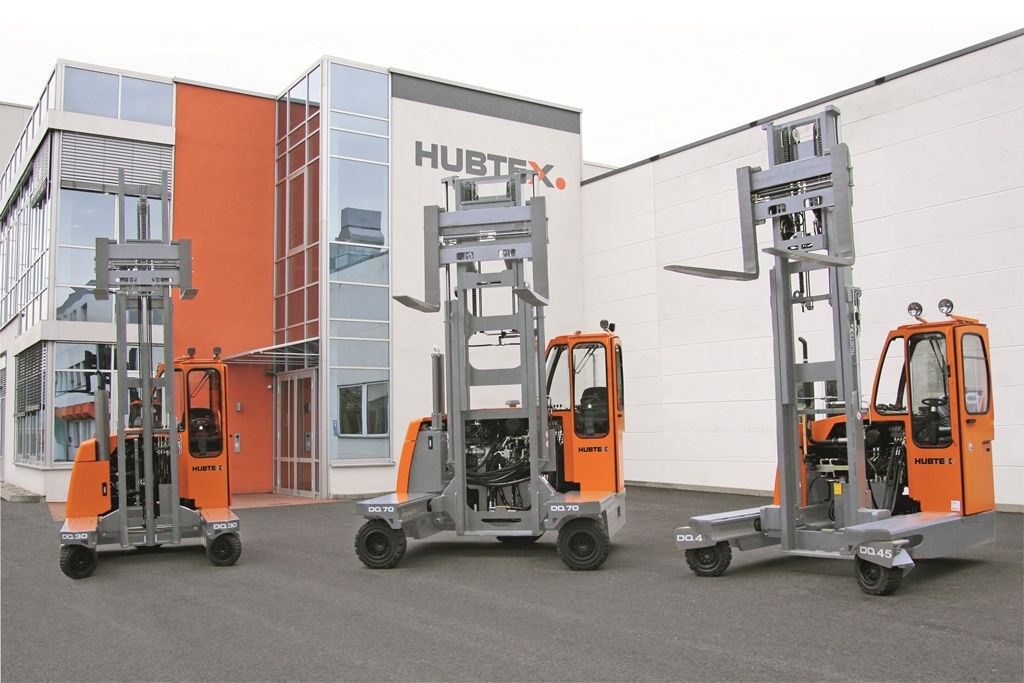
J. u. A. Frischeis GmbH relies on flexible HUBTEX electric multidirectional side- loaders for order picking and storage of large-scale timber plates. The quick
assembly order picking platform and the wire guidance are part of the project’s special characteristics.
Maximum delivery capacities and order service are a top priority for Andreas Winkler. For this reason, the subsidiary manager at J. u. A. Frischeis GmbH in Villach carefully planned the design of the ten metres high modern facility holding a capacity of 1,000 storage slots for timber plates. He took into account all levels of automation and load-handling systems to achieve an optimum flow of goods. In the end, Winkler opted for two electric HUBTEX multidirectional sideloaders with wire guidance which was deliv-ered at the start of 2013. The flexible concept is supplemented by a quickly installed platform which, if required, transforms one of the identical type MQ 70 series 2131 PU industrial trucks into an order picking unit.
The order picking platform with the width of 4,500 mm is designed for a capacity of 2.7 t and suitable for panels with dimensions of up to 3,000 x 2,070 mm. Without the plat-form, the MQ 70 is able to transport loads of up to 13 m in length and can carry a total weight of 7 t. “The removable platform offers us a maximum of flexibility and an opti-mum vehicle fleet for any kind of order situation”, Winkler remarks, adding that this consequently allows the company to offer customers short delivery periods. Every order received by 4 pm will usually be delivered on the following day. Up to around 60 items must be picked per customer or shipment. “We operate in a business that is strongly dominated by short deadlines, making pre-order picking almost impossible”, logistics manager Johannes Foessl explains.
As soon as the order picking platform, which was also provided by HUBTEX, has been installed, the MQ 70 can exclusively be controlled using one of the two operating panels on the platform. The electronics system has been designed for either one or two opera-tors. The operating panel facing the direction of travel is always activated to enable the best possible view. The two entry barriers lock electrically and a barrier on the loading area can be lowered manually. This guarantees safe access to the removal areas with a height of up to 7.5 m. “The safety aspect was preferential during the design and se-lection of the solution because commissioners must also be able to fully concentrate on the tasks ahead, even at the seventh shelf level”, Winkler emphasises. The figures speak for themselves: a team of two employees at Frischeis moves around 1.5 cubic metres of timber per hour. As a result, the Villach site is not only known as one of the most productive warehousing sites within the group of companies. Order picking directly from the shelf saves a significant amount of time. “Without a platform you would have to place the entire goods packages on the ground first before being able to pick the re-quired items for orders”, Foessl explains.
Inductive wire guidance brings additional benefits in terms of efficiency. Each of the ten rack aisles is equipped with an inductive wire milled into the centre of the flooring featur-ing transponders. Upon accessing the aisles, the wire is automatically detected by a high-frequency antenna fitted to the HUBTEX multidirectional sideloader. Then the elec-tronic controls of the MQ 70 take care of the exact positioning and alignment of the unit within the aisles with a width of merely 3.670 mm.
Thanks to the loaders’ precise controls, Frischeis was even able to do away with impact protection rails during construction of the system. However, the actual benefit lies in the vast amount of space gained: “The minimum distance on each side measures a mere 150 mm, thus allowing us to make ideal use of the width of the facility”, logistics man-ager Foessl says, adding “Thanks to inductive wire guidance, we were able to add three more rows of shelving compared with the driver-controlled solution.” The “invisible” solu-tion also means the aisles are much easier to clean than rail-based solutions, where cleaning is often very time-consuming.
In addition to the gained space and cleanliness of the facility, inductive guidance also means additional safety. As a result of the transponders having been integrated into the flooring, the industrial trucks can identify their current position and automatically reduce their speed upon leaving an aisle. “We have consequently reduced the risk of collisions significantly”, says Winkler, describing the system in his subsidiary which supplies around one hundred customers a day. Even though such high volumes require two-shift operation, the 80 V batteries with a capacity of 930 Ah cope with ease and they are on-ly charged at the charging stations during the night. As a result, Frischeis was even able to save the investment in replacement batteries.
After two years of use the HUBTEX high-tech solution has proven to be successful. This also applies to the maintenance and repair service that STILL GmbH has been providing throughout Austria over the past thirty years in addition to acting as the gen-eral HUBTEX importer. “The two MQ 70 are by far not our first HUBTEX products”, Fossl emphasises. The predecessor model has already been in use in Villach since 2007, where it has racked up more than 6,000 operating hours without any issues. “As a result, we are familiar with the engineers’ high levels of service quality and expertise and know they are also very committed to maintaining older machines and identify eve-ry fault within a short period”, Winkler says. The after-sales service is “particularly im-portant for the operation of multidirectional industrial trucks with a service life between 15 and 20 years”.
Fewer contacts
The proven cooperation between HUBTEX and STILL also has positive side effects for Frischeis as there are fewer contact persons in terms of the company’s industrial truck fleet. After all, one STILL RX 60-50 LSP 600 electric frontloader industrial truck is also in use at the Villach site. “It makes it easier for everyone involved if there is just one central supplier for several devices”, Winkler confirms. Michael Schulz, manager of the system technology and fleet management units at STILL in Austria, is delighted about this.
As a consequence of the positive experience in Villach, Frischeis opted for two HUBTEX multidirectional industrial trucks with inductive guidance for the Stockerau subsidiary in 2014. In comparison to driver-controlled solutions, the wire guided units are far superi-or, particularly in terms of operating aisle width (approximately 700 mm narrower per operating aisle) and safety by preventing impact damage to racks
and goods.
Background: J. u. A. Frischeis GmbH
J. u. A. Frischeis GmbH is Austria’s largest timber and timber material retailer. The company is run by its owners and was established in 1948 by Josef and Antonia Frischeis in Stockerau. Since then, the company has evolved from a local timber retailer to the internationally operating JAF Group, permanently stocking around 20,000 items at 53 sites in 16 countries. The company’s fleet includes 300 industrial trucks and 86 HGVs. In addition to Austria, JAF Group operates in Bosnia and Herzegovina, Bulgaria, Germany, Croatia, Poland, Romania, Russia, Serbia, Slovakia, Slovenia, the Czech Republic and Hungary. A workforce of around 2,200 employees generates an annual turnover of 570 million.