Renault Trucks Premieres Urban Lab 2
2nd December 2016
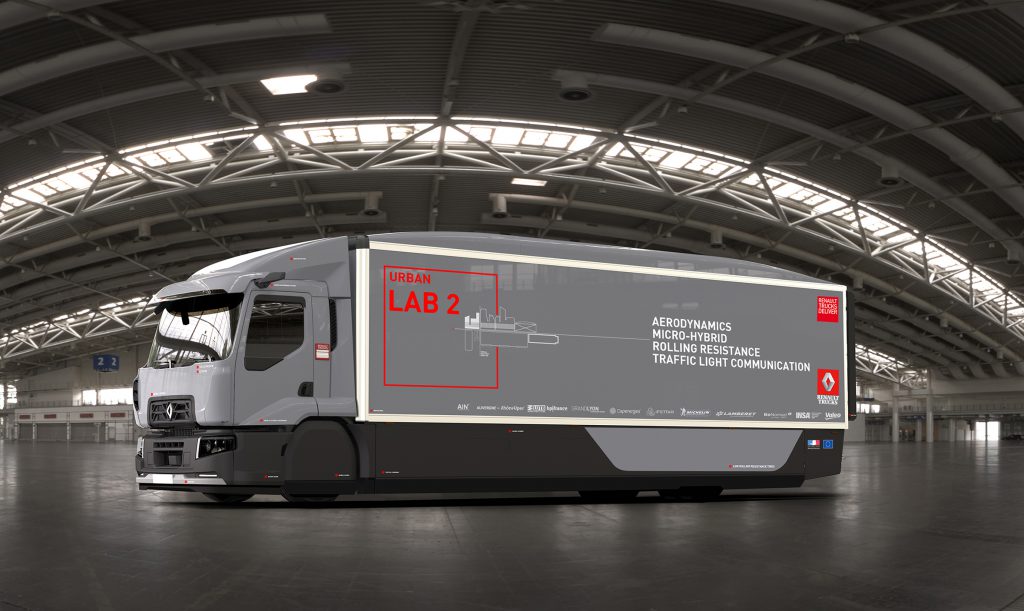
Renault Trucks has introduced Urban Lab 2 – its distribution concept vehicle – at this year’s Pollutec at Lyon’s Eurexpo exhibition centre, which ends today. Developed with six partners under the collaborative Efficient Distribution Truck (EDIT) project, the vehicle combines innovative technology in aerodynamics, hybridisation of the engine, tyres and vehicle-infrastructure communication to achieve potential fuel savings of up to 13%.
Whereas Optifuel Lab 1 and 2 were experimental vehicles dedicated to Research and Development for Long Distance transport, Urban Lab 2, designed using a 19-tonne Renault Trucks D WIDE Euro-6, targets the urban and regional distribution sector.
The aim is to offer accessible innovation by 2020, focusing on four key areas: aerodynamics, driveline, connectivity and tyres.
Aerodynamics
To reduce the aerodynamic drag of the Urban Lab 2 – and therefore its fuel consumption – engineers worked on airflow throughout the vehicle. Lamberet and Renault Trucks adapted the cab, chassis and refrigerated body to the recommendations of aerodynamic specialists, whilst meeting the regulatory and operating requirements of temperature-controlled transport.
The first step involves reducing the front surface area: “The refrigeration unit is normally located above the cab”, explained François Savoye, Energy Efficiency Strategy Manager at Renault Trucks. “On Urban Lab 2, we decided to position it in the wheelbase of the vehicle to free up space overhead and optimise the body/tractor link to lower the body and improve airflow. This meant we could incorporate a roof deflector shaped to provide seamless continuity with the body.
Redesigning the interior architecture of the refrigerated body has made a marked improvement in the shape of the roof, without adding to the height. As for the sides of the vehicle, these are fitted with textile side deflectors. “We have used a PVC-coated textile for the first time”, François Savoye added. “When stretched and fitted on the side protectors, it provides a light, effective and economic system.”
Lateral airflow is also boosted by streamlined wheels and the fitting of rear deflectors that are perfectly in keeping with the architecture and continuity of the tailgate. These deflectors are angled so as to reduce depression in the slipstream of the vehicle and do not require any manual operation when handling the doors. The access step is completely covered thanks to a mobile guard opened by door extensions that provides a seamless continuity between the upper and lower sections of the cab. Ground clearance is further optimised by the addition of flexible components, thus optimising air flow in the understructure.
In addition, replacing wing mirrors with a system of profiled cameras and internal feedback screens also helps reduce vehicle air resistance.
Stop&start
To reduce fuel consumption, Urban Lab 2 also proves innovative in its engine design, with a system combining Stop&Start and micro-hybrid technology, developed in partnership with Valeo.
The Stop&Start system cuts the engine when the vehicle comes to a stop (i.e. at a red light) thereby reducing fuel consumption. In addition, the micro-hybrid system recovers ‘free’ energy, such as energy generated during foot lift or braking, via a high-power (48 V) reversible electric machine. This energy can be used to drive the electrical accessories of the vehicle or reduce the mechanical power required by the thermal engine. Renault Trucks has also been working with the Lyon INSA to reduce friction in the front face of the engine in order to optimise the overall efficiency of the micro-hybrid system.
Connectivity
For Renault Trucks, drivers play a key role in reducing fuel consumption. This is why Urban Lab 2 features technology to help them with their driving by connecting the vehicle to infrastructures.
Working with the company BeNomad, engineers have developed special navigation software that to provide this connectivity. For each journey, the GPS suggests the most efficient route that uses the least fuel, estimating both the predicted journey time and fuel consumption. This software has been configured to take not only fuel consumption into account, but also, and above all, the operational constraints of a distribution vehicle.
Finally, Urban Lab 2 is connected to infrastructures to optimise driving through green lights. When Urban Lab 2 approaches traffic lights, it receives information from the lights and the system calculates if it is more efficient to brake or accelerate, when conditions and regulations allow. This therefore limits the amount of stop-start driving, which has such a high impact on fuel consumption.
The traffic modelling expertise of LICIT has helped Renault Trucks to effectively integrate the effect of traffic on fuel consumption.
Tyres
Already a partner on the Optifuel Lab 1 and 2 projects, Michelin is again working with Renault Trucks to develop energy-saving tyres specially designed for distribution vehicles.
“The objective of these tyres is to further reduce rolling resistance, without negatively impacting other performance criteria, such as safety, grip or longevity”, explained Jean-François Cordonnier, Truck Pre-development Manager at Michelin.
To this end, Michelin has deployed a wide range of technologies, in particular Infini-Coil technology, to guarantee tyre endurance and safety. Firstly, the self-generating tread ensures a lasting grip throughout the life of the tyre and secondly silica is used as a reinforcing agent in the tread to improve the compromise between longevity and rolling resistance.
Finally, Renault Trucks and its partners have set themselves the ambitious target of reducing fuel consumption by 13% compared to an equivalent Renault Trucks D WIDE. The vehicle was tested for the first time on a closed circuit in November 2016 and will be road tested in Bordeaux from February 2017 onwards.
The results will be presented at the end of the project, which is scheduled for 2018.