Road Safety: See it, Say it, Sorted
12th September 2024
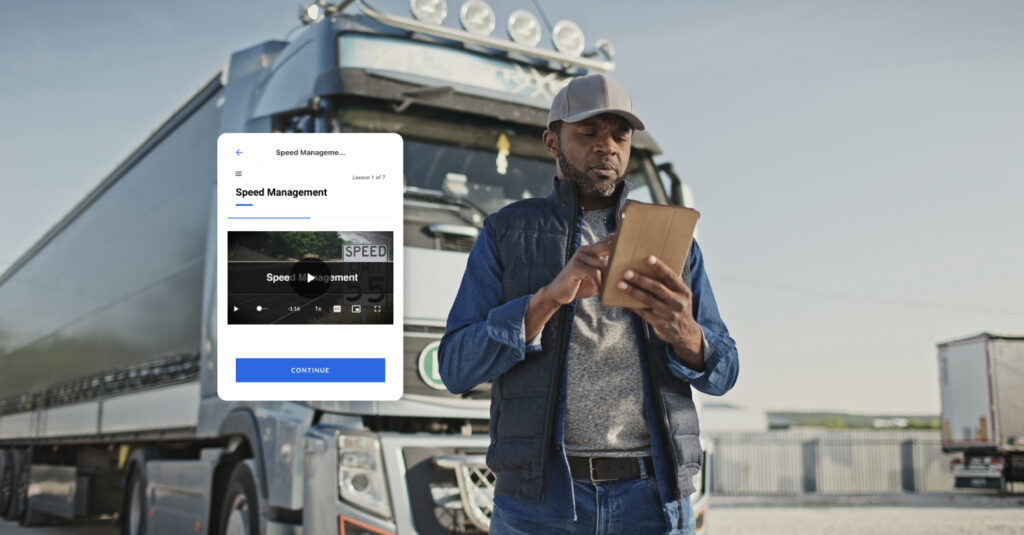
Data insights on road safety lead to action. At Samsara’s Beyond event in Chicago David Priestman learned how transport businesses can work smarter.
Chicago is a mightily impressive city. The construction of canals and then railroads made it the perfect location for trade and Chicago became the dominant port for wood in North America, with miles of lumber yards along its riverside, receiving timber from across the great lakes. Feats such as reversing the course of the river, reclaiming land from Lake Michigan and building the first skyscrapers followed. Workers flocked from everywhere, warehousing and stockyards boomed. A fitting venue, then, for discussing logistics.
Samsara’s CEO, Sanjit Biswas, has positioned the company and its AI and IoT technology to assist transport operators with challenges such as cargo detecting, trailer location, reefer monitoring, fuel saving, EV adoption, telematics and, above all, road safety. He pictures the service as a ‘flywheel’ – a virtuous circle for customers. AI creates the insights, using Samsara’s operational data and images, which leads to recommended actions for driver coaching, asset utilisation, EV suitability and emissions.
Over the last 12 months Samsara’s platform was used for 60 billion miles of driving, 75 billion API (application programming interface) calls and 9 trillion data points. DHL are a major customer and has reported a reduction in significant accidents by a quarter, with a halving both of the cost of accidents and of driver turnover. Impressive, given that DHL considered its fleet to be safe before switching to Samsara. “We’re just getting started,” declares Biswas, as applications in other sectors, such as construction and agriculture, are sought. With 290 integration partners Samsara try to make it easy to get set-up.
Same driver pool
Brakes Food distribution, part of Sysco, has had 1500 Samsara-equipped trucks for nearly two years. Prior to that Brakes used CCTV to monitor drivers, but could only do 10% of the fleet at a time, with little feedback, no real statistics and time delays for taking out the hard drives to look at the footage. “It was telematics without context,” explains Mike Cox, head of Health & Safety, “you might find bad driving but we want to be proactive, not reactive. We’re all fishing in the same driver pool.”
With Samsara, events are delivered to line managers instantly. “We thought we didn’t have a mobile phone problem,” adds Cox, “but we spotted 40 in the first month alone. We expected just 2! If you’re a 3PL not using AI and think you don’t have a phone usage problem think again,” he advises. When Brakes trialled Samsara one driver was caught watching a film on an iPad and checking his phone. Not only was he dismissed by Cox, the driver was also reported to the police.
Now Brakes analyses harsh breaking and turns. “With incidents we know if the driver is telling us the truth,” Cox states. “We can have better conversations with drivers as we can see the context. Sometimes it’s complicated, but we have these conversations within 24 hours.” The company’s insurance costs are down by 90%, on-road events down 40%, cost-per-claim down 10%. “Overall it’s less work for managers,” he concludes, “we can spot natural harsh turns, speed bumps, potholes etc. Extra work on screen is better than going to the vehicle to retrieve the hard drive.”
Tag your assets
A new product unveiled at Beyond is the Asset Tag. The size of a key fob (see picture), it is very durable. The tag uses Bluetooth to ping any Samsara gateway device in the vicinity. As all other devices are cellular and GPS-based, providing constant connectivity, the Asset Tag can piggyback on that network to provide exact location updates for high-value items in transit, giving cloud-based visibility. It has a 4-year battery life, no door or moving parts and can be applied to totes or pallets.
Samsara tested it by freezing, dropping and even striking with a golf driver club – the tag remained intact and functioning. On a 2000 mile test trip one Asset Tag was picked up by the Samsara network 1500 times, with 200 ‘pings’ a day. The tags are being manufactured in Mexico at scale. “Creative customers will find their own solution for them,” VP or Product Platform Sean McGee told me.
Let’s go
British electrical appliance online retailer AO has a national distribution centre in Crewe plus local depots, operating a fleet of 1000 commercial vehicles. Switching to Samsara from a telematics provider, “the demo was an eye opener,” according to Holly Beveridge, AO Commercial Business Partner. “Before switching members of the public would complain to us about bad driving twice a week, but it’s much less now.”
Fraikin provide a full-service contract hire fleet to AO, equipped with Samsara devices. “Fraikin gives us access to Samsara as part of a value-added service,” Beveridge explains. “This was the key moment when we realised that the most effective way of reducing our vehicle repair bills would be to leverage Samsara.” AO report a £2.2 million saving overall, including insurance cost reductions. Spending on tyres and new windscreens is down as a result of better driving. Fuel spend and engine idling are also lower.
AO’s drivers are self-employed and the logistics operation has seasonal peaks. Next day delivery is standard, with service, installation and recycling of old appliances offered. “We handle bulky products and heavy payloads,” Beveridge informs, “there’s little automation. Goods are sack-barrowed from the loading bay.” Driver coaching used to take days, with weekly meetings typical. Each depot has a driver manager. “Now we have the driver name (not just the vehicle registration number) and can do digital walkarounds. We get vehicle alerts for speeding and harsh events. Initially there were lots of alerts, now its fewer. We call the driver when an alert happens as we have 2-man crews which makes it safe.”
AO are trialling Samsara’s dashcams, to add them to the tech used. “We’re taking drivers on a journey,” Beveridge says, “rather than imposing it. Drivers are not keen but we’ll persuade them it’s in their interest too. We still have accidents, but they’re not as big.”
Safety first
Samsara tech is also being used for forklift fleet inspection checks, using the ‘Connected Forms’ App for safety and compliance needs. Accidents trigger a report and workflows are automatically assigned, using ‘Connected Training’ which has customised courses and quizzes. Biswas told me, “we cover operational assets, including all materials handling equipment. Safety inspections are a big use case. This is part of our expansion into lots of different vehicles and we’re thinking globally.”
New APIs launched this year include lane departure warning, drowsiness/fatigue and forward collision alerts. The core set of safety training provided by the platform is based on the various alerts, which also include heavy braking, phone use, seatbelt use, tailgating and fast acceleration. This triggers training on specific behaviour and reduces the time involved for it as it’s done remotely. Alerts are meant to ‘nip problems in the bud’, rather than recalling drivers to their depot. Immediacy is best for corrections. The platform capture all the alerts in one place, so all the data is there.
Outcome is more important than hardware. “Can we get to the driver before they have an accident?” Ingo Wiegand, Samsara’s safety expert, asks. “We make that possible by spotting good drivers and bad drivers easily. We can exonerate innocent drivers on the spot due to the video footage,” which creates a good butterfly effect. The dashcam has been refreshed, for new installations and there are camera connectors for side cameras on trailers. Blindspot detection technology may be added soon. One Mexican 3PL customer, Trayecto, has a panic button for drivers, to provide security and reassure them that they are not alone. Fewer thefts means higher driver retention.
It’s Electrifying
Most Samsara customers deploy multiple solutions, including TMS and telematics. “We don’t expect to be the only tech supplier to them,” states Robert Bales, Director of Product Management. “We don’t offer order management or TMS but we overlap on work modules, routing, driver applications and digital proof-of-delivery.”
Electric vehicle adoption is an opportunity for Samsara to add further value. “Investment in charging sites is open data,” Bates adds. “We help customers see the state of the battery, charging profile and battery degradation, advising them what percentage charge is optimal to enable journeys to be completed quicker.” Europe is ahead of the USA on EV uptake. Distances are shorter and user incentives higher, with better charging facilities. It makes sense to switch to EVs, says Bales, if your fleet is mainly operating shorter routes and charging at your own warehouses and DCs, rather than opportunity charging.
One new EV is Freightliner’s eCascadia HGV truck, which can be 80% charged in 90 minutes, with a range between 155 and 230 miles. Samsara provide EV suitability analysis, looking at a vehicle’s usage, mileage and fuel cost per mile to advise which ICE trucks and vans are least efficient and should be switched to EVs first. It can make direct comparisons from mpg to kWh, or a threshold can be selected, such as a cost per mile cap to see how many vehicles should be changed. Autonomous vehicles (AVs) is the next horizon, but is not forecast to eliminate driver shortages and may bring additional costs plus the obvious challenges of charging and crossing borders. Platooning AVs in convoy is probably years away.
Deploying Samsara implies a certain amount of engagement for the transport operator. There’s a minimum of 1-2% fuel saving. Heavy users with large fleets can make 6-7% fuel and idling reductions. On a fleet of 1000 that is a big saving. Drivers can even be incentivised financially to help achieve these results. Business-savvy Chicago would approve.
similar news