Supply Chain Resilience from Transparency and Collaboration
25th June 2024
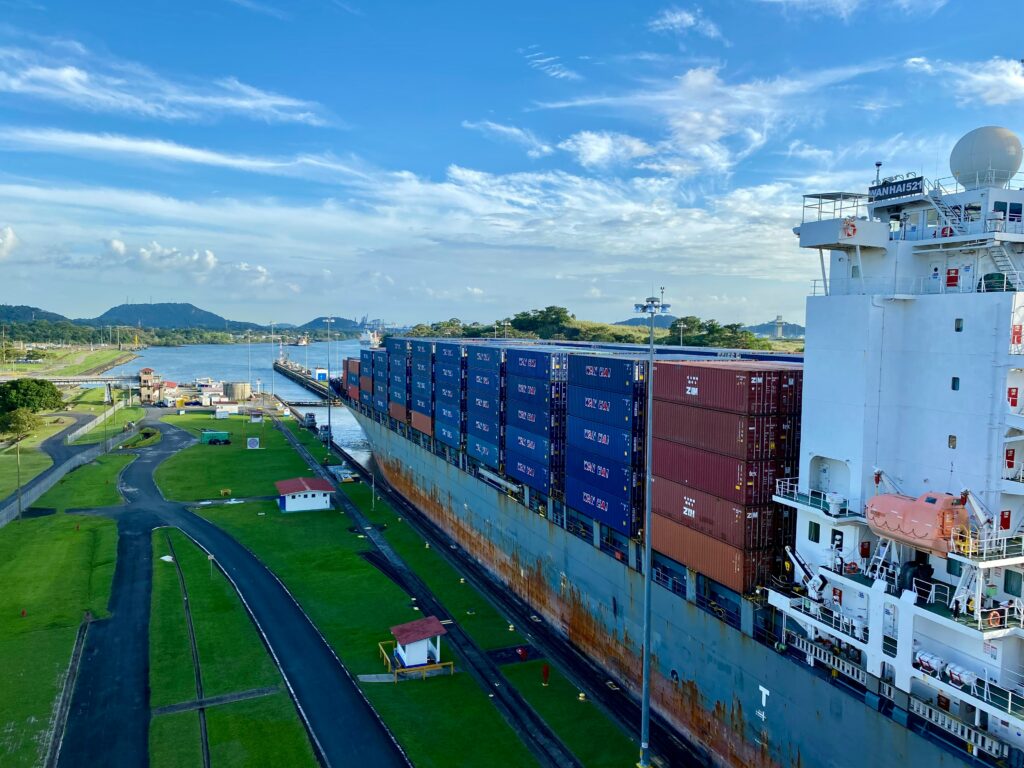
Cost savings used to be at the top of supply chain managers’ agendas. However, in an increasingly volatile world, the design of robust value chains is increasingly becoming the focus of decision-makers. This is likely to remain the case for the future, writes Ralf Duester, Managing Director, Setlog GmbH.
Many ships are currently avoiding the Suez Canal because of the Houthi rebels. In 2023, extreme drought caused ships to jam at the Panama Canal. According to Setlog Managing Director Ralf Duester, companies need to establish robust and transparent supply chains due to supply chain problems like these so that they can react quickly.
A non-maneuverable container ship causes a bridge in Baltimore to collapse, Houthi rebels hijack ships in the Red Sea, storms flood the desert city of Dubai: reports like these give many supply chain managers sleepless nights. Supply chains are interrupted overnight, freight capacities and equipment are missing without warning. Supply chain managers need to find new transport routes, ports or suppliers, plan with longer lead times, produce earlier or faster or select more expensive modes of transportation. Geopolitical, economic, ecological and technical changes put global supply chains under pressure at short intervals – or even interrupt them.
As a result, the topic of supply chain resilience is at the top of the agenda for supply chain managers. Things were different a few years ago. Take Germany, for example: the “Trends in Logistics & SCM” study conducted by the German Logistics Association BVL in 2023 shows that cost pressure was the most important topic for decision-makers in 2016, but in 2023 it only ranks fourth. Cybersecurity is now the top priority, followed by digitalization and the shortage of skilled workers. Many measures in terms of cyber security and digitalization contribute to making supply chains more robust.
Resilience can basically be divided into two components: the operational, reactive component and the strategic, proactive component. The latter requires top managers in companies to fundamentally rethink their decisions. They need to find ways to strengthen the robustness of the supply chain through decisions in sourcing, product design, production, planning and logistics.
Basically, all companies need to think about supply chain resilience. Companies with global operations – such as automotive suppliers, semiconductor manufacturers or consumer goods specialists – are particularly affected by supply chain disruptions. To make matters worse, importers of fast-moving consumer goods (FMCGs), for example, have no choice but to purchase their products in Asia or countries outside Europe for cost reasons. If they were to produce in Germany, they would generally not be competitive.
Storms, disasters, war: although a large number of negative events occur every year, it is frightening to see how slowly companies can react to such disruptions to supply chains – even in highly industrialized countries. Current surveys show that in Germany, for example, on average only one in ten companies is able to respond to a serious disaster within 24 hours. Although there are exceptions – for example in the oil and gas industry – this average value shows the risks that many companies take on a daily basis.
One reason for long response times is the fact that companies still use Excel lists as the basis for managing their supply chains – and there are quite a few of them: More than a third of German companies rely solely on this program, supplemented by emails and frantic phone calls to obtain information, which is then re-entered into the existing Excel lists or merchandise management systems.
In general, statistics show that larger corporations in particular have strengthened their supply chains with the help of various instruments. Smaller companies and SMEs are lagging behind – or are still at the beginning of a transformation phase.
The good news for everyone is that there is a whole range of measures that companies can use to achieve success relatively quickly. Supply chain champions usually start with an analysis, looking at the areas in which risks are suspected and what impact these could have on the company’s performance. Those responsible then define the levers that best address the identified risks. They take a cross-functional approach: This is because the causes are generally not to be found where the consequences of supply chain weaknesses appear.
Companies are well advised to turn a whole series of screws in parallel in order to strengthen their resilience in the areas of supply chain and procurement. These include in the area of supply chain: Segmentation of the supply chain; Strengthening of integrated planning; Inventory management according to risk criteria; Diversification of freight forwarders; Re-evaluation of the network design.
The following applies to purchasing: Multi-sourcing strategies for critical components; Creation of supplier risk profiles; Development of regional suppliers; Closer cooperation with suppliers; Creating transparency in terms of actual supplier capacities.
To accomplish all this, the development and use of centralized, digital cross-company solutions and data exchange between different systems are an important step in enabling collaborative, partnership-based cooperation with business partners globally. Nowadays, this is easily possible with intelligent API interfaces, so that the silo of management or the ERP system can be broken down and easily linked with intelligent solutions and the data flow is optimized.
The issue of skilled labour shortage also shows that these methods are the only way to avoid redundancies in day-to-day work, make better use of skilled employees’ working time and make faster, higher quality decisions.
Incidentally, supply chain champions pay more attention to product design and production, because these areas in particular can lay the foundations for a more robust supply chain. They consistently tackle issues such as modular design, component standardization, raw material composition and supplier origin.
However, in order to make supply chains more robust in the long term, companies need to do more than just implement individual measures. In order to achieve cost efficiency, growth and resilience at the same time, SCM managers should rethink and redefine the decision drivers in the supply chain. As a rule, costs, quality and time or service level are regarded as decision drivers in supply chain management. The configuration of a supply chain takes a position on these drivers, which cannot be improved at the same time. Leading global players consider resilience to be a key decision driver – alongside sustainability and agility.
Some companies mistakenly assume that there is a conflict between the drivers of costs and resilience. The following aspects are important in this context: The aim of resilience is also to avoid costs in the medium and long term. However, this does not necessarily have to involve short-term costs and redundancies. Many initiatives to strengthen supply chains make it possible to increase cost efficiency at the same time, so that resilience levers can certainly be implemented, for example with the secondary condition of cost neutrality.
Many supply chain strategists segment supply chains. Sometimes very successfully. If, for example, higher stock ranges are to apply to critical parts, actual and target stock levels must be analyzed. This is a simple way for companies to achieve inventory savings for less critical parts. Other levers relating to visibility and supplier integration generally achieve more efficient processes, more precise planning and automation options.
Despite the change in many people’s minds, the fact remains that resilience and risk management with a focus on supply chains are still being neglected from an organizational perspective. Competent teams can ensure cross-functional coordination and establish communication channels for faster risk identification. In this context, the best of the best simulate various crises, also known as “war gaming”. Unfortunately, many companies lack the required knowledge of which future scenarios could occur due to negative geopolitical, economic and ecological events. However, knowing which scenarios could happen forms the basis for developing suitable countermeasures and thus strengthening the resilience of the supply chain.
Over the next few years, digitalization and artificial intelligence will make even more tools available that can strengthen the robustness of supply chains. Whatever these solutions look like, they are anything but superfluous. The topic of resilience is not just hype, it will be a constant concern.
read more
Improve Supply Chain Resilience in Infrastructure Project Delivery